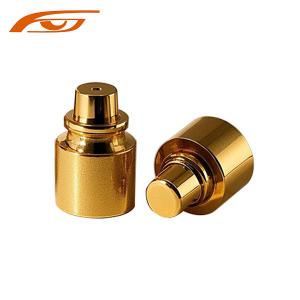
Add to Cart
Custom Gold Plating Electroplating CNC Machining Fabrication Service Metal Parts
Technical Parameters
Brand Name | Selection |
Part Name | Custom Electroplating Zinc/Nickel/Chrome/Gold Plating Parts |
Place of Origin | Guangdong, China |
Service | One-Stop Metal Fabrication Service/ Surface Treatment Service |
Material Capabilities | Aluminum, Zinc Alloy, Stainless Steel, Copper, Brass, etc |
Cost | Depend on your project. Usually Competitive Price |
Certificates | ISO9001:2015 |
Packing Details | Usually PE bag, outer carton.We can packing as your requirements. |
Surface Finish | Electroplating, Nickel/Chrome/Zinc/Gold Plating, etc |
Lead Time | 3~4 Weeks |
Custom Electroplating Parts
Electroplating is a surface finishing process that involves the deposition of a thin layer of metal onto a substrate (usually a metal or plastic part) using an electric current. The process is commonly used to improve the appearance, corrosion resistance, wear resistance, and other properties of the base material. In electroplating, the metal that will be plated is dissolved from an electrode (the anode) and then plated onto the workpiece (the cathode) through the application of an electric current.
How Electroplating Works:
1. Preparation: The substrate (the part to be plated) is cleaned to remove oils, dirt, oxidation, and any other contaminants. This is often done by chemical cleaning, abrasive cleaning, or ultrasonic cleaning.
2. Plating Bath: The workpiece is submerged in a solution called the electrolyte bath, which contains a metal salt of the metal to be plated (e.g., nickel, gold, silver, chromium) and other chemicals to improve the process.
3. Electric Current: A direct current is passed through the electrolyte bath, causing the metal ions to be reduced and deposited onto the surface of the substrate. The anode is typically made of the same material as the metal being plated (e.g., a gold anode for gold plating).
4. Deposition: The metal ions are attracted to the negatively charged substrate (cathode), where they gain electrons and settle as a thin metallic layer.
5. Finishing: After plating, the part may undergo additional treatments, such as polishing, coating, or heat treatment, to enhance the quality and durability of the electroplated surface.
Common Electroplating Materials
1. Nickel: Provides a smooth, corrosion-resistant, and decorative finish.
2. Chrome: Known for its hardness, wear resistance, and bright appearance.
3. Gold: Used for electronics and decorative purposes due to its conductivity and aesthetic appeal.
4. Zinc: Offers excellent corrosion protection for steel parts.
5. Copper: Often used as an undercoat to improve adhesion and conductivity.
6. Silver: Highly conductive, making it ideal for electrical components.
Support and Services
At Shenzhen Selection Hardware Technology Co., Ltd., we provide comprehensive surface finishing services designed to enhance the appearance, durability, and functionality of metal and plastic parts. With advanced equipment and years of expertise, we ensure every component meets the highest standards of quality and precision.
Our Surface Finishing Capabilities
1. Anodizing: Regular and Colored Anodizing: Improves corrosion resistance, hardness, and aesthetics. Available in various colors like black, red, gold, blue, and custom shades.
2. Electroplating: Includes nickel, chrome, zinc, and gold plating for enhanced surface protection and appearance. Ideal for applications requiring conductivity or decorative finishes.
3. Powder Coating: Durable and uniform coating in a wide range of colors and textures. Provides excellent protection against wear, scratches, and corrosion.
4. Polishing:
Mirror Polishing: Achieves a high-gloss finish for premium aesthetics.
Brushed Polishing: Adds a sophisticated satin texture to surfaces.
5. Sandblasting: Creates a matte or textured surface, enhancing grip and visual appeal. Prepares surfaces for subsequent treatments like painting or anodizing.
6. Painting and Coating: Custom colors and finishes for functional or decorative purposes. Includes wet painting and specialty coatings (e.g., anti-rust, anti-fingerprint).
7. Silk Screening and Laser Engraving: For logos, patterns, or markings with high precision and durability. Perfect for branding and product identification.
8. Heat Treatment and Black Oxide: Improves wear resistance, strength, and corrosion protection for functional parts.
Why Choose Our Surface Finish Services
1. One-Stop Solution: Comprehensive services from raw material processing to final surface finishing.
2. Customization: Tailored finishes to meet unique requirements in appearance, texture, and functionality.
3. Advanced Technology: ISO9001:2015-certified processes using cutting-edge machinery.
4. Experienced Team: Skilled technicians ensuring consistent and high-quality results.
5. Diverse Applications: Suitable for industries like automotive, aerospace, medical devices, electronics, and more.